Objectives of the Product
The consequences of levee failure are huge. Sea level rise, extreme weather such as hurricanes, storms and drought events around the world continue to lead to critical flood defence failures resulting in tragic losses of life and the devastation of large areas. Water managers, insurance companies, real estate development organizations and other (government) agencies responsible for water safety need cost effective tools to better manage levee failure risks. The traditional way of detection risks of levee failures is difficult, expensive, and covers only parts of water barriers at a certain point in time.
Especially for experts that have responsibilities for safety and prevention, Sat4Flood provides a service that indicates stress factors of levees based on the most actual satellite data that can be implemented anywhere in the world. Sat4Flood visualizes the risks of levee failure based on the most recent Earth observation satellite data. This development combines the innovative technologies of satellite high-resolution soil moisture data with InSAR deformation data and other Earth observation data sources. Sat4Flood indicates the flood risk based on levee failure mechanisms such as overtopping and saturation, and enables high quality, large area covering, cost effective, and frequent monitoring based on satellite Earth observation.
Customers and their Needs
Targeted customers are water authorities (direct responsible organizations to manage and monitor levees), municipalities, cities and regions/counties (responsible for the safety of citizens), crisis management/relief organizations and insurance companies (important for them to understand the risks of levee failures), real estate development (in relation to the impact of levee failure on the value of an area), mining companies (monitoring of tailing dams), international organizations such as United Nations and World Bank and international engineering firms with focus on water and civil engineering (to extend their product portfolio).
Targeted customers who are responsible for water safety need cost effective tools to better manage levee failure risks. They are involved in the activity by indicating their user needs and participating in a proof of concept to test and pilot the service.
Levee monitoring is a global challenge. Geographically, Sat4Flood starts rollout in the Netherlands, then continue in Europe. For worldwide rollout, a network of engineering forms and IT companies is targeted.
Targeted customer/users countries
Product description
Sat4Flood is a levee risk monitoring service based on Earth observation data. The main building blocks are soil moisture data (from optical) and deformation data (from InSAR). The application combines these two main building blocks with other satellite data such as water levels and meteorological data, and then indicates and visualizes the flood risk based on levee failure mechanisms such as drought and saturation. A web portal enables effective dissemination of information and user-friendly interfacing with customers.
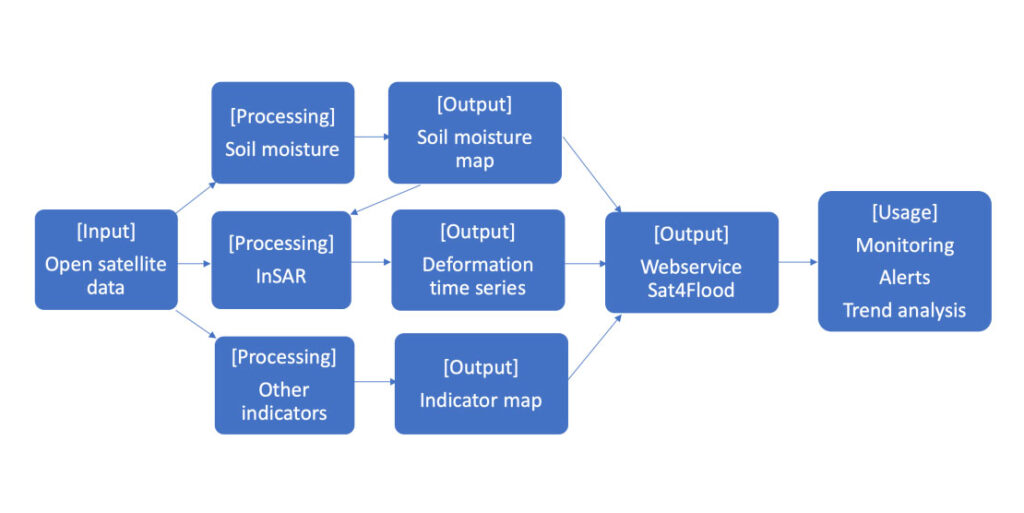
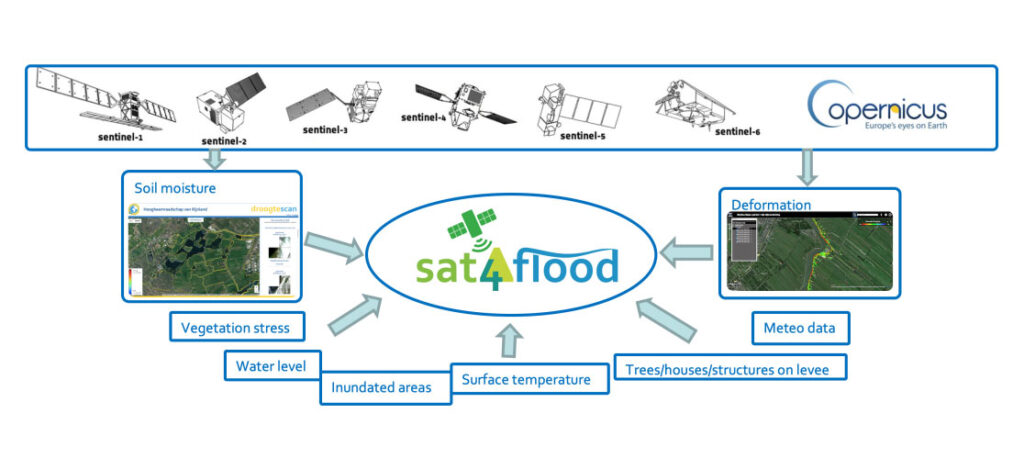
Added Value
- Continuous and reliable monitoring of the levee of interest;
- Large area covering and frequent monitoring;
- Deployable anywhere on the globe without the need to visit the side physically
- Monitoring for emergencies as well as under normal circumstances;
- Easily adaptable to specific needs of the customer;
- Weight of risk factors tailored to the specific context of the levee interest and user needs;
- A cost-efficient way of monitoring the risks of levees; cost effective due to the smart usage of open satellite data;
- Detect trends by using historical data sets.
Current status
In March 2021, the project was successfully concluded with a final review. The main objectives of the project were to develop Sat4Flood, demonstrate the service with users, and make the service commercially ready. All three objectives have been realized: The consortium has developed Sat4Flood and demonstrated the system with 3 organizations on 12 locations. There is a clear need to monitor levees and identify risks of levee failures. Sat4Flood uses existing Earth observing satellite systems, which has huge advantages: cost efficiency due to the use of open access data, coverage of the whole levee, and acquisition of key information without the need to go physically to the levee. The product is commercially ready, which means that Sat4Flood can be incorporated into identified customer workflows. During the pilot-demonstrations we have learned how customers want to work with Sat4Flood and how Sat4Flood can be integrated into their workflows. Now, at the end of the activity, we have identified customers and market opportunities, developed an integrated service to monitor risk indicators of levees, and we have implemented pilot-demonstrations with (potential) customers and partners. Those elements enable us to further rollout and upscale the service.